02.06.2018 17:00:00
|
Star Helps British Healthcare Provider Save Thousands of Pounds by Becoming More Efficient
GLASGOW, United Kingdom, June 02, 2018 /PRNewswire-PRWeb/ -- Star Refrigeration has developed a good relationship with the company over the past ten years, and gained a reputation for the design and maintenance work carried out at other sites across the country. This led to the customer taking out a three-year maintenance contract with Star Refrigeration Operations Group, which has proved to be a worthy investment.
When Star engineers arrived on site recently, they found that the customer's ammonia plant was overcharged with oil due to incorrect setup. Soon after taking over the contract, the plant's expansion valves were replaced in order to regulate gas back to normal working pressures and working levels. Star's proactive and planned maintenance routines had no impact on the customer's operation.
An important part of Star Refrigeration's aftercare work was to ensure that the British pharmaceutical company's ammonia plant was up to date with current regulations. The team of engineering experts also implemented site SAP routines to ensure that air conditioning systems were routinely assessed and subject to regular and consistent maintenance.
Additionally, plant performance was reviewed on a regular basis to ensure it was working at optimum conditions.
Working together with the customer's energy supervisor Star Refrigeration monitored the plant energy usage and quickly picked up when the plant was not operating at maximum efficiency. Through the installation of air conditioners with timers in all of the site's central offices, Star was able to reduce the customer's energy bills by £8,000 per annum.
Star's good performance during the initial contract period resulted in the customer renewing their aftercare contract for another three years. In addition, the customer trusted Star Refrigeration's Aberdeen team with a new project to design and install a brand new plant for an extension to their facilities.
Furthermore, the customer also requested Star's services to assess the need for an Ethos system, a performance optimisation and energy management system, for their ammonia chillers. The award-winning Ethos system is a new scheme developed by consultants Star Technical Solutions (STS) which identifies efficiency problems and can save plant owners thousands of pounds in electricity bills - typical energy savings of 30% to 40%-. It effectively measures the gap between how the plant is operating and how it should be operating and identifies corrective actions to reduce the gap.
The Ice Co, Asda, BrewDog and Campbell's Prime Meat all use Ethos in order to address common maintenance activities, improve the control strategy as well as replace inefficient equipment.
Niall Murphie, Chief Engineer of BrewDog, said, "Our expansion over the past 5 years has been rapid and we've needed to ensure our equipment is ready to meet demand. We commissioned STS to measure operation and performance of our existing chillers through Ethos so that we could gain a better insight into refrigeration load and spare capacity ahead of increasing production".
Malcolm Dufton, Property and Energy Manager at The Ice Co & Logistics said of Ethos, "Energy consumption is a large operating expense for us. Add on charges increasingly diminish the control we have on our electricity costs. Therefore, we focus on reducing energy usage and already the improvements identified on one system will reduce its energy cost by 10%, encouraging us to roll out the service to our other systems and sites."
"A key feature for us is the online monitoring dashboard, it gives our managers and engineers clear real-time visibility of all our connected systems health and performance and allows them to drive energy savings and preventative maintenance."
Campbell's Prime Meat also employed Ethos to assess future investment. Offering positive feedback of the system, Darrin Leslie, Factory Manager for the company, said, "We planned to expand our production facility and were not sure whether our existing refrigeration plant had sufficient capacity to handle the additional cooling duty required. Rather than taking a risk or buying additional equipment that maybe wasn't necessary we employed Star Technical Solutions (STS) to assess our site's cooling demand over a 2 week period. The assessment revealed that our existing equipment could comfortably handle the new production load. Star's appraisal allowed us to capitalise on surplus capacity and avoid the unnecessary purchase of new equipment."
To enable the Ethos service, STS installs sensors and an Ethos panel to the customer's systems. This information is sent via the built-in 4G mobile connection to a web portal, where it is assessed by software and a team of refrigeration consultants. Customers can access a customised online dashboard from where to check details about plant performance and corrective actions including monetary value resulting from undertaken these actions.
Star Refrigeration Operations Group also offers national 24-hour technical support for the customer from nine branches across the UK. This includes design, maintenance, service, contracting and spare parts as required. Star Refrigeration Operations Group is now pioneering the use of condition based monitoring for industrial refrigeration end users and delivering improved efficiency, greater reliability and lower total cost of ownership.
To find out more about Star Refrigeration and the groundbreaking Ethos system, visit: http://www.star-ref.co.uk/
SOURCE Star Refrigeration
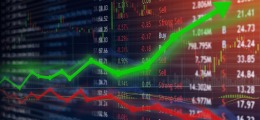
Wenn Sie mehr über das Thema Aktien erfahren wollen, finden Sie in unserem Ratgeber viele interessante Artikel dazu!
Jetzt informieren!