18.04.2019 19:08:17
|
DGAP-News: Kibaran Resources Limited: EcoGraf Study Delivers Downstream Development
DGAP-News: Kibaran Resources Limited / Key word(s): Miscellaneous EcoGraf Study Delivers Downstream Development Global New Supply of Environmentally Sustainable Battery Graphite for the Lithium-ion Battery and Smart Technologies Markets Kibaran Resources Limited ("Kibaran" or the "Company") (ASX: KNL), is pleased to announce the successful completion of engineering studies based on the optimised graphite purification flowsheet. The Company plans to fast-track the commercialisation of its proprietary battery (spherical) graphite purification technology. HIGHLIGHTS - Updated 20,000 tonnes per annum ("tpa") engineering study to produce battery (spherical) graphite for the lithium-ion battery market confirms the key aspects to support development and commercialisation: - Highly competitive / operating costs - Environmentally sustainable chemical purification process provides a clear alternative to existing supplies produced with toxic hydrofluoric ("HF") acid - /consistently delivers high purity battery (spherical) graphite products that achieve stringent customer chemical and physical quality specifications - Robust financial metrics for 20,000tpa production plant: - Initial investment of US$64m - Pre-tax NPV10 of US$194m ($268m) and IRR of 49.8% - Annual EBITDA of US$42m ($58m) - NPV and annual EBITDA increased by 34% and 38% respectively compared to 2017 estimate - Development de-risked through extensive customer product qualification program and staged development to 20,000tpa - Long-term demand for battery (spherical) graphite expected to increase rapidly with Roskill forecasting EV penetration rates increasing from 2% in 2018 to 25% by 2025 - Demand ex-China expected to break through 100,000 tonnes of battery (spherical) graphite in 2020 - Increasing focus by electric vehicle and energy storage manufacturers on ensuring ethical raw material supply chain - Combined pre-tax net present value of the Company's potential mining and downstream graphite businesses is US$405m ($559m) EcoGraf DOWNSTREAM BATTERY GRAPHITE BUSINESS Kibaran's /development involves initially establishing an Asia-Pacific manufacturing plant close to existing markets, commencing with the production capacity of 5,000 tonnes of battery graphite and increasing to 20,000 tonnes per year (or more) as required to meet customer demand. Over the last number of months GR Engineering Services Limited ("GR Engineering") has re-designed the /production flowsheet to incorporate the results of the German purification optimisation program and also completed an updated estimate of 20,000tpa capital and operating costs. The GR Engineering capital cost estimate for 2019 is based on construction of a new /production facility in the Asia-Pacific region, using existing sea and land transport infrastructure, water and power supplies. Equipment quotations have been obtained from suppliers in Asia, Europe and Australia. The update has resulted in a faster ramp-up phase to meet the growing demand requirements of battery anode manufacturers, which also enables the Company to increase the capital efficiency of the new /development. The total estimated cost to construct a 20,000tpa facility (including a 10% contingency) is US$64m compared to the 2017 estimate of US$66m (refer announcement 5 December 2017). Completion of the study is an important milestone in Kibaran's vertically integrated growth and diversification strategy. CAPITAL AND OPERATING COSTS
Table 1: Capital estimate based on the staged expansion to 20,000tpa
Table 2: Operating estimate
KEY FINANCIAL PARAMETERS Financial Summary The results of the engineering study have been used to update the / financial model, demonstrating a highly attractive return on investment. Table 3: Key metrics, assuming a 60% gearing rate, 20,000tpa battery graphite production facility and 20 year operation are as follows:
12019 terms net of CIF costs The investment has a pay-back period of less than 4 years and capital and operating costs adopted in the engineering study were prepared on the basis of independent quotations submitted by equipment vendors and service providers. Major operating expenditures are power and reagents, with the potential for future savings from the use of renewable energy supplies and processing refinements to optimise chemical usage efficiency. The updated study has resulted in NPV and annual EBITDA increasing by 34% and 38% respectively compared to the 2017 estimate. Graphite Pricing and Assumptions The Company has adopted a conservative long-term pricing model that is based on discussions with anode and battery manufacturers in Asia and an assessment of various global forecasts for energy, electric battery and electric vehicle growth rates over the next 10-20 years. Table 4: Pricing assumptions (after US$25/t CIF costs)
Cost Comparison to Existing Supply and Purification Methods Cost competitiveness is a major consideration to securing sales as China is the benchmark for current graphite anode material pricing. The operating cost base for existing supply of battery (spherical) graphite produced using toxic hydrofluoric (HF) purification processes is estimated between US$2,000 - $3,000 per tonne. / products are expected to be cost effective compared to existing HF supplies and other chemical and thermal purification methods, due to an efficient processing flowsheet, lower energy requirements and use of readily available chemical reagents.
PROJECT IMPLEMENTATION SCHEDULE GR Engineering has developed a staged implementation plan for /, achieving a production capacity of 20,000tpa in 2.5 years.
BATTERY GRAPHITE FORECAST DEMAND, SUPPLY AND PRICING Competitive Positioning for Electric Vehicle and Energy Storage Markets Feedback from lithium-ion battery anode manufacturers indicates that demand from e-mobility and energy storage markets will continue to grow strongly. By 2021 almost half of global battery graphite material is expected to be sourced from new suppliers in Asia and Europe, reducing the existing dependency on toxic HF purification. Currently all battery (spherical) graphite is produced in China using HF acid. It is estimated that 250kg of HF is required to produce 1,000kg battery (spherical) graphite, creating increasing environmental and safety concerns for regulators. The focus on ensuring ethical and environmentally sustainable supply chains which is already evident in cobalt markets, is expected to support the adoption of /products which is cost competitive with existing supply and green. Recent examples of this change include: - BMW Group adopts new approaches for a more sustainable battery cell supply chain and plans for greater transparency on battery minerals for German battery manufacturers; - Sonnen selection of lithium-iron phosphate cathode chemistry to avoid cobalt and other toxic heavy metals; - Volkswagen Group alliance with Swedish battery manufacturer Northvolt to form the European Battery Alliance which supports battery cell manufacturing in Europe given Volkswagen have stated a sustainable value chain is equally important as competitive pricing; and - Contemporary Amperex Technology Co's sustainable development commitment statement as part of its procurement strategy. Forecast Demand The long-term battery (spherical) graphite demand remains positive with Benchmark reporting EV penetration rates increasing from 2% in 2018 to 25% by 2025, requiring approximately 600,000 tonnes of battery (spherical) graphite, more than six times the volume currently produced. In addition to EV market demand, energy storage is expected to drive new demand, Bloomberg New Energy Finance ("BNEF") reports that battery storage costs have fallen by more than one third over the last 12 months, primarily due to a 35% reduction in the cost of lithium-ion battery storage. BNEF stated that batteries co-located with solar and/or wind projects are starting to compete in many markets and without subsidy, with coal and gas-fired generation for the provision of 'dispatchable power' that can be delivered on demand to the electricity grid. Forecast Pricing Benchmark reports current pricing for purified battery (spherical) graphite ranges between US$3,100 and US$4,400, with the market comprised of three standard product categories, based on particle size distribution. Prices for battery (spherical) graphite products increased during 2018, with pricing for standard grade rising from US$3,000/tonne to US$3,600/tonne. Future prices are expected to be supported by a number of key developments: - A restriction in supply, due to increasing environmental pressure on both natural flake and synthetic battery graphite producers in China; - Limited availability of high-quality battery grade graphite to satisfy customer requirements for increasingly stringent product specifications; and - Increased pressure to reduce the use of existing HF acid purification processes due to both Government and customer environmental concerns as more provinces within China adopt bans on the use of this widely used, but toxic acid in current graphite purification processes.
/ PROCESS DESCRIPTION Overview The / process to produce battery (spherical) graphite is a two staged process involving mechanical shaping followed by purification: - Mechanical shaping involves micronising and spheronisation using existing technology to increase material density, which a key requirement for battery performance. - / purification process is a chemical process which does not use toxic HF acid, which has historically been the method for producing battery (spherical) graphite from natural flake graphite. - The / process can also be successfully applied to the fines bi-product of the spheronisation process and to large flake graphite. Carbon content exceeds 99.95% if the purification process is made with the / methodology. - The /purification is a unique, staged process where impurities are removed through the creation of new chemical compounds that are soluble in either water or chemical reagents. All steps in the process are completed in a manner that preserves the important physical properties of the graphite spheres, such as low specific surface area, high tap density and narrow particle size distribution. The result is a sophisticated process with efficient usage of chemical reagents, that produces very high purity anode material.
Mechanical Shaping - Micronising and Spheronising The processing route selected for the micronising and spheronising of the graphite flake is a continuous process using pulverisers (mills) in series. Several trains will be used, each train has a capacity of producing spherical graphite between 2,500-3,000tpa each. The trains are identical, with each train containing six micronising and eighteen spheronising mills. Each spheronising mill is in circuit with an air separator, spheronising cyclone and baghose. The air separator allows for the control of product sizing with the coarse size fraction from the air separator feeding the next spheronising mill in series. Purification Process The spherical graphite is subject to a chemical purification process to upgrade the graphite content to >99.96% graphite. In the first step, the bagged spherical graphite is mixed with a chemical solution. The mixed product is heated at low temperatures. Under precise heating conditions, the impurities bind with the reagents, creating new chemical compounds which are soluble, either by water or by chemicals. The process involves multiple stages of chemical treatment, washing and filtration. Each of the manufacturing steps are conducted in a precise manner to preserve the physical properties specified by battery manufacturers.
PRODUCT QUALIFICATION PROGRAM AND FEEDSTOCK MATERIAL The overall optimisation program was extended to incorporate additional test work to support the Company's plan to develop and commercialise /as a stand-alone downstream business. The additional work extended the program by several months and included: - preparation of further product samples for supply to battery manufacturers under collaboration arrangements for product development and potential investment; - testing of /purification processes on non-Epanko sources of natural flake graphite; and - an assessment of the potential application of the /purification techniques to produce high purity graphite for other carbon technology applications. In the last 2 years the Company has produced over 80 graphite product samples as part of the product accreditation program, including both battery graphite and high purity flake products and has met the product specifications of battery anode manufacturers and battery market participants. This product testing and accreditation process is a critical precursor to secure offtake commitments and a number of organisations have subsequently expressed interest in potential joint development of /production facilities. During the optimisation program, 10 global graphite feedstocks were also evaluated using the / purification process to identify a range of available natural graphite feedstocks to enable the downstream processing business to commence independently of the Epanko Graphite Project in Tanzania. Table 5: Graphite samples from global producers tested using /
Table 6: Feedstock for /battery (spherical) graphite plant
CURRENT BATTERY GRAPHITE SUPPLY China is the only producer of commercial quantities of natural flake battery (spherical) graphite which uses HF acid to achieve 99.95% carbon grade. Hubei and Shandong provinces are the largest producing areas and there is increasing pressure on producers due to environmental and occupational health & safety regulations. HF acid is critical for the production of high purity flake and battery graphite in China, with approximately 250kg of HF acid required for every tonne of battery graphite in order to remove the high levels of silica (SiO2) impurities of up to 40% contained within natural graphite ores mined in China. The HF acid contributes significantly to the cost of producing such products due to its high input cost (which has doubled in the last 12 months) and the costs associated with HF acid safety and environmental management. It is estimated that HF acid accounts for approximately 60% of the total production cost of these graphite products. Purification Methods There are several known techniques for producing high purity graphite to more than 99.95% carbon content. Table 7: Purification methods to produce battery (spherical) graphite
Battery Anode Specifications Each anode manufacturer has individual product specifications determined through their unique anode requirements and to achieve market acceptance purified spherical graphite must satisfy extensive physical and chemical performance criteria that include: - Purity carbon grade (%) - Quantitative level of impurities - Particle size distribution - X-ray diffraction - Specific surface area - Tap density Table 8: Quality analysis for Kibaran's standard battery (spherical) graphite SPG15 (D15 micron)
Importance of Battery (Spherical) Graphite in Lithium-ion and other Battery Technologies Graphite is a major component of a lithium-ion battery, which in turn comprises approximately 40% of the cost of an electric vehicle. The majority of the cost of a lithium-ion battery results from the cathode (+ve) and anode (-ve) cells. Anode chemistry is a combination of battery (spherical) graphite produced from natural graphite, synthetic graphite and silicon. Natural graphite is less expensive than synthetic graphite and provides a higher energy density, while synthetic graphite is more customisable and stable due to its uniformity.
During the 8th International Advanced Automobile Battery Conference held in Mainz, Germany in March 2018, leading battery scientists predicted that existing lithium-ion battery technology will continue to be the basis for most applications for the foreseeable future. It will be further developed, focused on the production of an 'advanced' or 'second generation' lithium-ion battery that will continue to require graphite as the main material for the anode cell. Key conclusions from the conference are that: - Electric vehicle manufacturers expect lithium-ion batteries will continue to dominate the e-mobility market; - Solid state batteries may enter the market in the future, however many technical challenges will need to be overcome; and - Significant new investment by automobile manufacturers in lithium-ion battery powered EV supply chains is expected to last many years due to the cost and long lead times for such commitments and the associated after-market vehicle maintenance obligations to consumers. Graphite will be required as a key component as it's a conductive material for use in the solid-state battery and in other leading battery technologies for the energy storage market. Graphite is also key component in the polar plates, which distribute the energy inside fuel cell and redox flow batteries. Lithium-Ion-Battery Fuel Cell Redox Flow Battery
ESTABLISHING A GLOBAL BATTERY GRAPHITE SUPPLY CHAIN The GR Engineering study evaluated a number of potential manufacturing locations in Africa, Europe and the Asia-Pacific region, comparing the cost and availability of power and water infrastructure, skilled labour, equipment and processing reagents. Increasing demand and diversification in supply sought from South Korean, Japanese and European battery manufacturers has resulted in the Company developing a multi-hub strategy for establishing multi-hub /manufacturing facilities. In conjunction with its evaluation of Asia-Pacific plant locations, Kibaran is also considering how it could support Australia's ambitions to become a regional lithium-ion battery manufacturing centre. Preliminary discussions have been held with Australia's largest energy companies, Federal and State Governments on the benefits of the unique /high purity battery graphite products. A range of mechanisms have been created by Government to incentivise Australian industry to develop lithium-ion battery capabilities, including the planned creation of WA's Lithium Valley within the Kwinana Strategic Industrial Area south of Perth and the Future Batteries Co-operative Research Centre, of which the Company is a founding participant. The Company is positioned to establish a sustainable, eco-friendly battery graphite business that meets the increasing requirements of lithium-ion battery manufacturers for more diversified and environmentally responsible supply chains. The continued production of battery graphite using toxic HF acid is inconsistent with these aspirations. The combined pre-tax net present value of Kibaran's planned upstream and downstream businesses is US$405m ($559m) (refer ASX announcement 5 December 2017).
For further information, please contact: INVESTORS MEDIA Andrew Spinks Paul Armstrong
18.04.2019 Dissemination of a Corporate News, transmitted by DGAP - a service of EQS Group AG. |
801999 18.04.2019
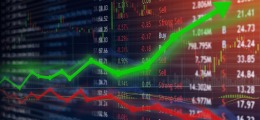
Wenn Sie mehr über das Thema Aktien erfahren wollen, finden Sie in unserem Ratgeber viele interessante Artikel dazu!
Jetzt informieren!
Nachrichten zu Kibaran Resources Ltdmehr Nachrichten
22.10.24 |
EQS-News: Technische Vorplanung für Epanko abgeschlossen (EQS Group) | |
22.10.24 |
EQS-News: Epanko Front-End Engineering Design Completed (EQS Group) | |
11.09.24 |
EQS-News: EcoGraf nimmt an führenden koreanischen und tansanischen Veranstaltungen in Perth teil (EQS Group) | |
11.09.24 |
EQS-News: EcoGraf Attends Leading Korean and Tanzanian (EQS Group) | |
19.08.24 |
EQS-News: EcoGraf: Neues zur Epanko-Darlehensfinanzierung (EQS Group) | |
19.08.24 |
EQS-News: EcoGraf: Epanko Debt Financing Update (EQS Group) | |
15.08.24 |
EQS-News: EcoGraf: Planungsskizzen der Epanko-Graphitaufbereitungsanlage abgeschlossen (EQS Group) | |
31.07.24 |
EQS-News: Quartalsbericht (EQS Group) |